Insulation Properties and Application
Insulating materials are an important part of energy-efficient construction and thermal insulation. The bulk densities [kg/m³] and the resulting thermal conductivity λ [W/mK] is the decisive parameter for assessing their properties.
Insulation thickness and R-value
Every insulation product needs a technical data sheet stating the methodology to which it was tested to, or an appraisal for the use in New Zealand. In order to comply with the requirements of the energy efficiency clause H1, the thermal conductivity [W/mK] of the insulation must be considered in connection with the layer thickness. It follows that with a low thermal conductivity, the insulation layers can be made thinner. In New Zealand typically the R-Value is provided for each product to make the application under the acceptable solutions easier.
Additional selection criteria
In addition to the insulation performance other properties such as the fire protection class, compressive strength or water absorption are taken into account. When sustainability measures are taken into account decomposability or the energy consumption in production (life cycle analysis) can be taken into account.
Types of Insulation (available, or most common in NZ in bold)
airogel
cotton
expanded glass
expanded perlite
expanded clay
flax
cereals (e.g. spelled husks, rye granules, straw)
grasses (reeds, cattails, meadow grass, seaweed)
hemp
Wood (wood fibers boards, wood shavings, wood wool, multi-layer boards)
calcium silicate
coconut
cork
clay
mineral fibers (glass and rock wool)
mineral insulation boards / mineral foam boards
phenolic resin hard foam board / resol resin board
polyurethane / PU (PIR, PUR)
polystyrene (EPS and XPS)
sheep wool
foam glass (slabs or crushed stone)
vacuum Insulation Panel (VIP)
cellulose
Hygrothermal considerations
How does water change insulation properties?
Water generally has a higher thermal conductivity than air. In the case of insulating materials the objective is to incorporate as high a proportion of air as possible into the materials. In the case of foamed products, this occurs in the form of pores. Permeable materials without pore spaces, such as insulating wool, can have an air content of up to 92% when dry.
Investigations (Europe) showed that the thermal conductivity of an EPS insulating material increased with consistent wetting. In a state of almost complete moisture penetration, the insulation achieved a thermal conductivity of λ = 0.6 W/mK. The investigation also showed that with 10% by volume of water in the insulating material, its insulating capacity was halved. The eight-centimetre-thick insulation board tested had roughly the insulating capacity of a four-centimetre-thick, non-moisturised board.
Using WUFI the individual performance of an assembly can be determined in detail and for a specific location. The material data for most components contain a function that adjust the thermal conductivity based on water content among other product specific material data, see image below for generic mineral wool.
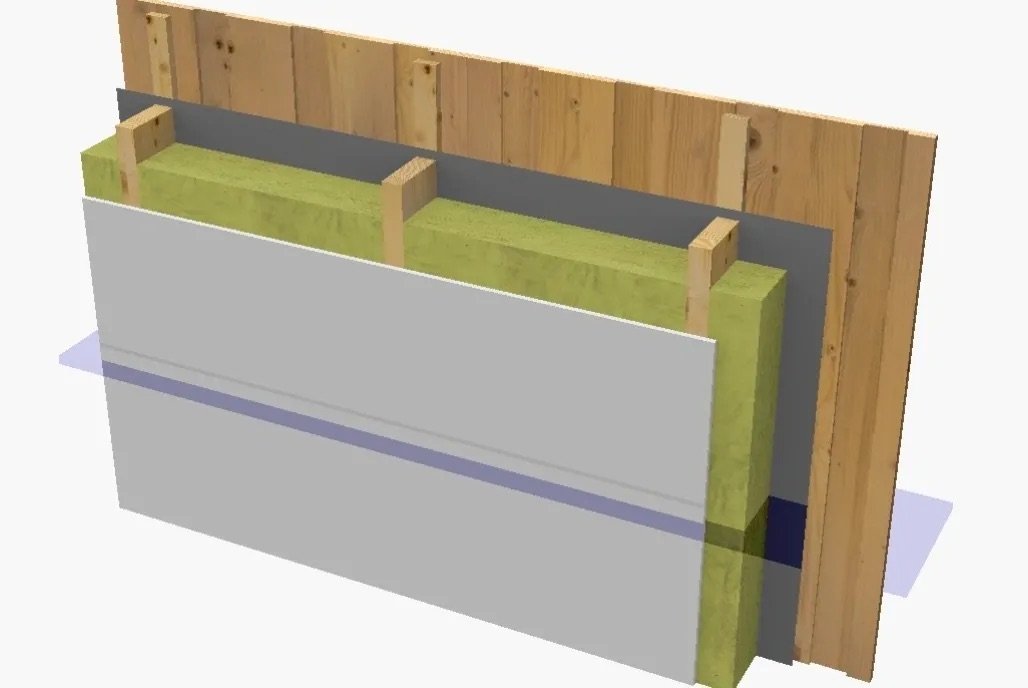
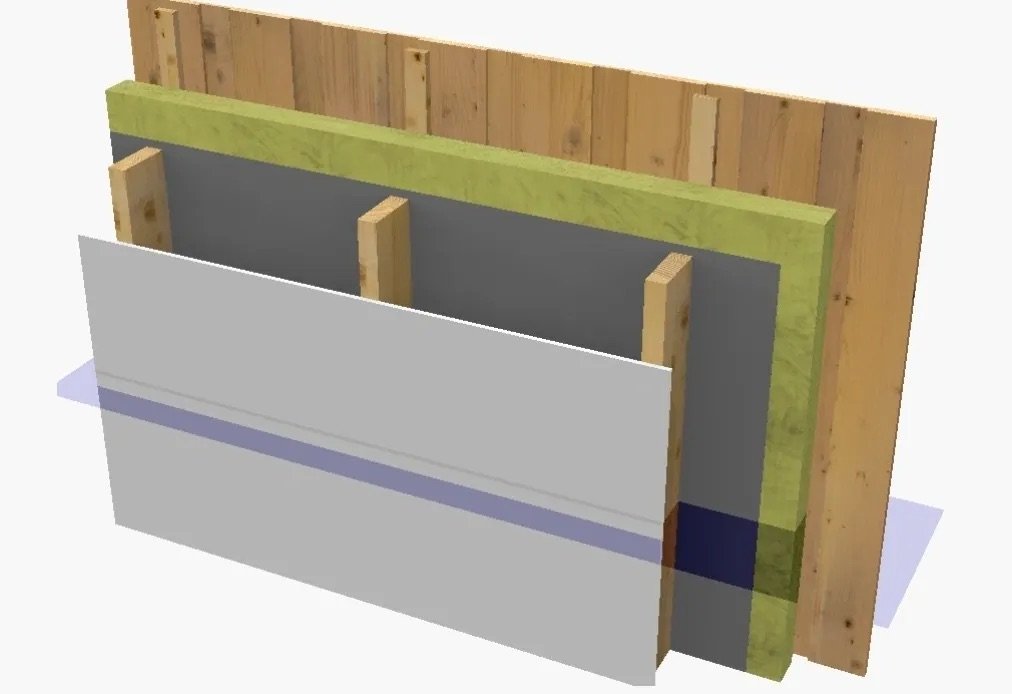
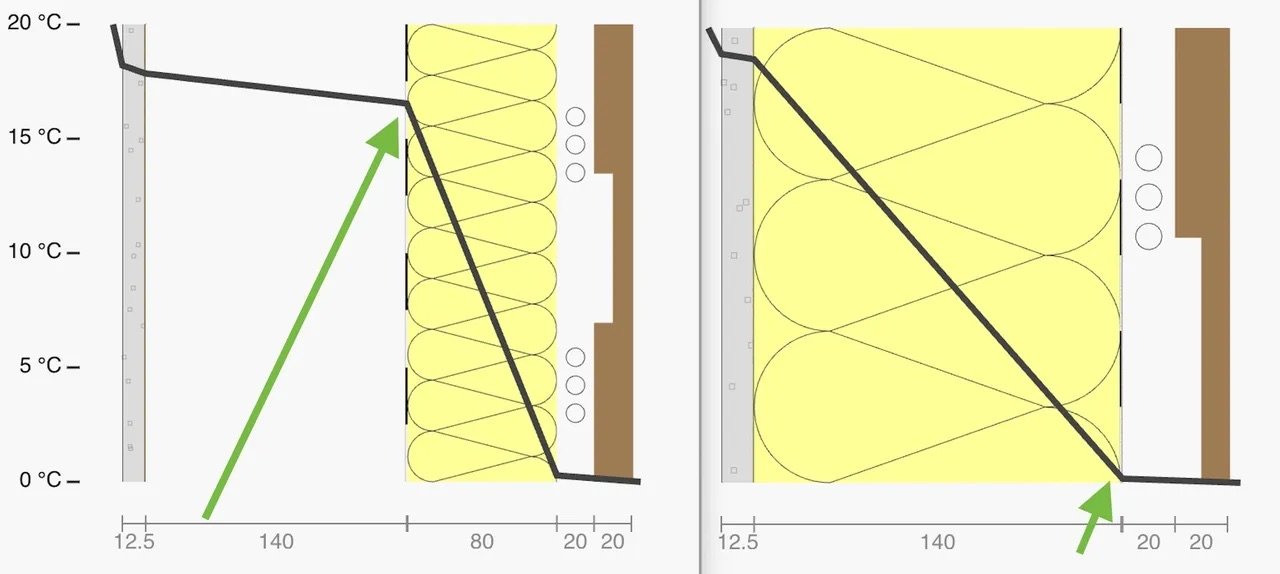
External insulation
External insulation has the advantage that thermal bridges are minimised and the overall energy efficiency is optimised. In addition external insulation offers the advantage that the load-bearing structure of the building is no longer exposed to temperature changes and thermal stresses in the component can thus be almost completely ruled out.
With reduced thermal bridging a balanced and comfortable interior climate can be achieved because the surface temperature on the inside of the walls is relatively high and almost corresponds to the temperature of the interior air. This separation allows for the internal structure to function as a heat storage which also works well for overheating protection especially with concrete structures.
Interior, or standard stud frame insulation
With this type of insulation the structure is completely at risk of temperature exposure on both side, exterior and interior, which is also increasing thermal bridging effects. These lead to increased heat flows which can result in the surface temperature falling below the recommended surface temperature of 12.6 °C in the transitions. This means that there is a risk of condensate forming on the cold surfaces which forms the basis for fungal infestation. At the same time if vapour control layers are installed improperly condensation water can form between the insulation and the cold component.
Hence vapour control is a vital part of interior insulation!
A look at the temperature distribution between both systems shows that the external insulation keeps the structure "warm".